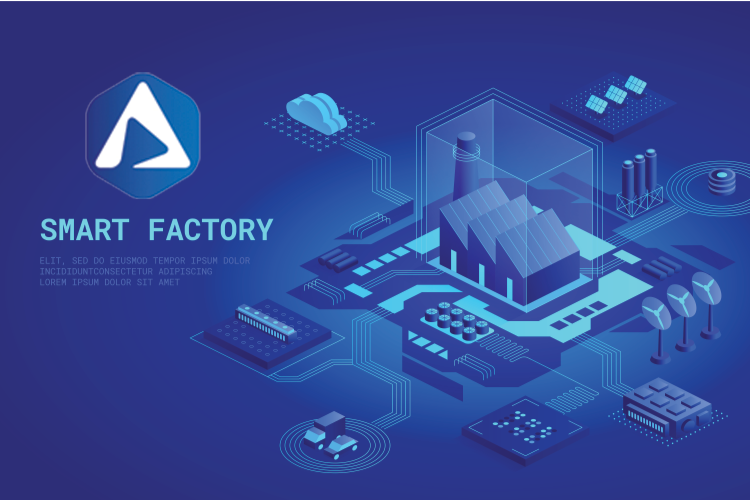
Smart Factory: a role Arania’s model for industrial transformation
Digitalisation is now firmly consolidated in the industrial universe, so technological efforts in the steel sector as a whole and the strategy in companies such as Arania are currently focused on making further progress towards future’s Smart Factory. Arguably, at the heart of smart industry is data: a huge amount of information being constantly collected and processed, both at small scale (in terms of individual pieces of equipment or small production units) and on a macro level (potentially involving an entire industrial group with factories spread around the world).
With the inclusion of new technologies based on big data such as AI, today we can extract both knowledge and value from this huge volume of available information. Benefits can be seen very quickly: optimisation of decision-making, automation of operations based on specific needs, improved ability to anticipate production cycles and increased flexibility to deal with any contingency, among others.
Companies in the technology and knowledge industries are a “close and friendly ally” for the development of digitalisation and automation of processes, the smart-updating of production and the surge of new advanced specific services related to connected products and machines. Once again, these firms have selected Arania as an example of industrial success to showcase the best practices in the transformation towards the factory of the future.
How can we incorporate digitalisation into factories to make them more competitive and efficient? This was the main subject of the conference [SMART FACTORY – SMART INDUSTRY] , a one-day event promoted by AceleraPYME and GAIA (Association of Knowledge Industries and Technologies) to present diagnoses, plans, methodologies and disruptive technologies focused on reaching the Smart Factory concept.
The Arania team is particularly pleased to participate in these seminars, where companies can meet and share their experiences, seeking to identify opportunities for progress in the productive transformation, especially by analysing the best practices for the digitalisation and automation of an industrial plant’s management, as well as the contribution of these technologies to a company’s competitiveness.
Iñaki Lopategui, Head of Engineering, Investment Projects and Manufacturing Technologies at Arania, presented his insights and explained the implementation of the Smart Factory at our cold-rolled steel plant in Amorebieta (Spain), an ongoing process that has been underway for several years, with different technological solutions integrated throughout all stages of the production chain.
But how to transform a whole company and modernise production processes, without stopping the activity? And how to take advantage of the existing physical assets while upgrading equipment? From the very beginning, Arania’s technological and industrial challenge was ambitious and promising, but also achievable, thanks to a coordinated effort carried out at all levels of the company.
Rather than a single technological project, the road towards a Smart Factory has been a full-scale industrial transformation process: implementation of the automated external coil storage system, autonomous intralogistics trolleys, deployment of the automated intermediate warehouse, fully automated product packaging…
Besides the above-mentioned actions (which are just some of the “visible” examples of this process), other ongoing operations are being implemented to boost efficiency and productivity in the factory, within the framework of a large-scale objective: converting a cold rolling mill into a Smart Factory by automating and computerising the entire production, thus achieving a state-of-the-art industry in terms of digitisation, manufacturing quality and intralogistics.
For instance, the innovative automated warehouse developped by Arania has been a project repeatedly highlighted as a successful model for the automation in the rolled steel industry, and presented at several events and conferences on industrial digitalisation.
Arania’s medium- to long-term modernisation process is mainly based on the successful incorporation of advanced technology. For example, we have reengineered the operating procedures at certain stages of production, most notably with the implementation of a MES (Manufacturing Execution System) software by enntte® , which allows complete control over resources, equipment and processes, starting from the receipt of raw materials up to the shipping of the finished product.
As an example, in addition to enntte®’s own algorithms, an AI module is being developed for the automated warehouse cranes with the purpose of managing the priority of movements and optimising the trajectories and task distribution for each crane. In summary, this means complete supervision of an entire industrial plant, resulting in benefits that apply to other complementary activities of the company and spread throughout the Arania Group .
So what are the results? A widespread increase in productivity, the optimisation of projects for automation, a higher level of operational efficiency, an increased capacity to react to unforeseen events, real-time monitoring of processes involving the entire plant… In addition, the traceability of products has also been strengthened, as well as the self-management of operations, culminating in a more efficient control of rejects and retrievals.
Now, Arania’s Smart Factory is moving forward: further steps in this venture include the incorporation of an AI-based algorithm in the factory’s processes, which will enable for higher levels of automation in decision-making. Therefore, it will be possible to improve the prediction of quality failures, as well as preventing production stoppages, optimising stock management and reducing the manufacturing lead time.
For more than 80 years, Arania has always been committed to technological innovation and progress, not only as fundamental drivers for economic growth, but also by integrating this restless and avant-garde spirit into the company’s industrial DNA.